Just-in-Time (JIT) Inventory Replenishment: Benefits & How It Works
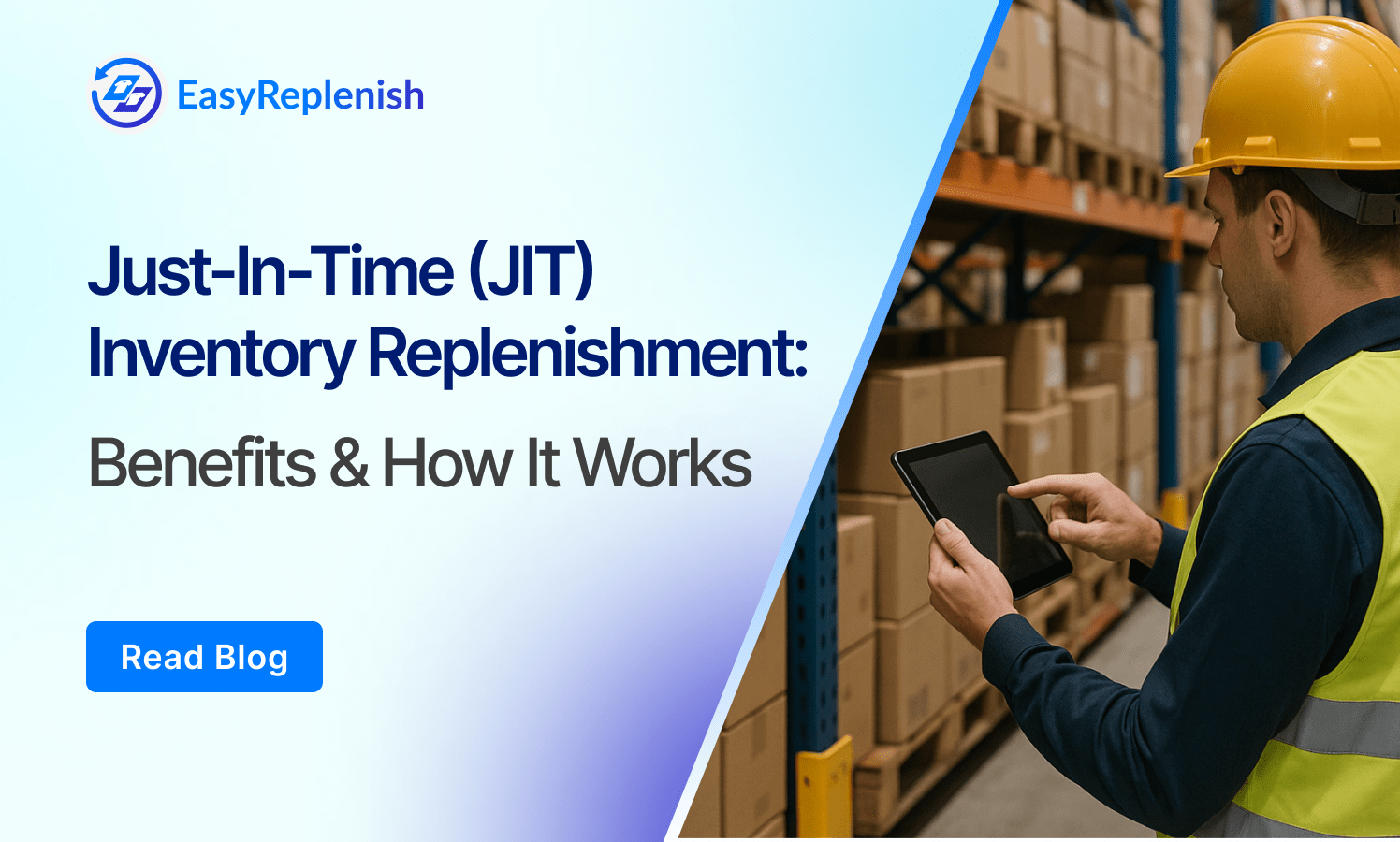
Holding too much inventory ties up capital, inflates storage costs, and often leads to dead stock. But understocking leads to missed sales and fulfillment delays.
That’s the balancing act every inventory planner faces—and Just-In-Time (JIT) inventory replenishment is one approach designed to solve it.
JIT is not about rushing or running on thin margins. It's about building a responsive, demand-driven system where inventory arrives only when it’s needed, not weeks in advance. Done right, JIT reduces waste, improves working capital, and makes your supply chain sharper and leaner.
In this guide, we’ll break down:
- What JIT replenishment actually means (and what it doesn’t)
- How it works step-by-step in real-world operations
- The benefits and risks businesses need to consider
- Where JIT works best—and where it can break down
If you’re aiming to run leaner, faster, and more cash-efficient operations, understanding how JIT replenishment works is a smart place to start.
What Is Just-In-Time Inventory Replenishment?
Just-in-Time (JIT) inventory replenishment is a supply chain strategy where inventory is received only as it’s needed in the production or order fulfillment process, rather than being stocked in advance.
The goal is to keep inventory levels as low as possible without disrupting operations, allowing businesses to reduce carrying costs, avoid overstocking, and respond more flexibly to actual demand.
At its core, JIT shifts the mindset from “stocking up just in case” to “ordering just in time.” Instead of purchasing or producing goods weeks or months ahead of anticipated sales, JIT systems rely on accurate forecasting, reliable supplier relationships, and tight coordination between demand signals and supply responses.
This model was famously pioneered by Toyota in its manufacturing plants, but today it’s widely adopted by retailers, distributors, and DTC brands looking to streamline operations and preserve working capital.
How Just-In-Time Replenishment Works: The Process
Just-in-Time inventory replenishment isn’t about simply reducing stock—it’s about creating a synchronized, real-time inventory system where supply matches demand with as little friction, delay, or excess as possible. Here’s how the JIT process works in a well-executed environment:
1. Demand Signals Trigger Replenishment
The entire JIT system starts with actual demand—be it a customer order, a low-stock alert, or a production requirement. These signals are captured from sales platforms, ERP systems, or POS systems and act as real-time triggers for inventory movement.
Unlike traditional models that rely heavily on forecast-based stocking, JIT reacts to real consumption, allowing businesses to avoid overestimating demand.
2. Automated Reordering or Procurement
Once a demand signal is registered, the system automatically initiates a replenishment order—either to a supplier or an internal warehouse. This automation is typically driven by inventory management systems that calculate reorder points dynamically, based on current stock levels and lead times.
The goal is to eliminate lag between consumption and replenishment, ensuring that new stock arrives exactly when it’s needed, without manual intervention.
3. Lean Stock Movement Across the Supply Chain
Under JIT, inventory doesn’t sit idle. It’s ordered in smaller, more frequent batches and moves quickly through the supply chain. Warehouses are no longer long-term storage hubs—they operate more like transit points, turning inventory around quickly.
This keeps storage costs low, minimizes stock aging, and reduces the risk of holding obsolete items, especially in fast-moving categories like fashion or electronics.
4. Fast, Reliable Supplier Fulfillment
Because JIT operates with minimal buffer stock, the system relies heavily on suppliers who can deliver with short lead times and high consistency. Businesses often work with local or nearshore suppliers, and build strong procurement relationships with clear expectations, backup options, and performance SLAs. A single delay can ripple through the system, so trust and reliability are foundational.
5. Continuous Monitoring and Realignment
Even the most well-designed JIT system needs constant oversight. Businesses monitor inventory positions, demand shifts, supplier reliability, and lead time variability in real time.
If a shipment is delayed or demand spikes unexpectedly, the system needs to respond fast—either by rerouting inventory, expediting orders, or adjusting reorder thresholds. The system is dynamic, not static, and that’s what keeps it resilient.
JIT vs Traditional Replenishment Models: Key Differences
1. Replenishment Trigger
- JIT: Replenishment is triggered by actual demand (sales or consumption).
- Traditional: Replenishment is based on forecasts, reorder points, or scheduled intervals.
2. Inventory Levels
- JIT: Maintains minimal inventory—just enough to meet current demand.
- Traditional: Keeps buffer or safety stock to cover demand fluctuations and delays.
3. Lead Time Sensitivity
- JIT: Highly sensitive to supplier lead times and disruptions.
- Traditional: More forgiving due to extra inventory on hand.
4. Carrying Costs
- JIT: Significantly lower carrying costs due to leaner stock levels.
- Traditional: Higher carrying costs from storing excess or inactive inventory.
5. Forecast Dependency
- JIT: Relies less on forecasts; operates in near real-time.
- Traditional: Heavily forecast-driven; demand estimates determine replenishment.
6. Supplier Relationship
- JIT: Requires fast, reliable, and often local suppliers.
- Traditional: More flexibility with longer lead times or global sourcing.
7. Operational Risk
- JIT: Higher risk of stockouts if disruptions occur.
- Traditional: Lower risk, but at the cost of efficiency and capital lock-up.
8. Best For
- JIT: Businesses with predictable demand, high inventory holding costs, or fast production cycles.
- Traditional: Businesses with long lead times, unpredictable demand, or capacity for holding extra stock.
How to Transition to a JIT Replenishment Model
Shifting to a Just-in-Time replenishment system is not instant—it requires systemic alignment across demand planning, procurement, supply chain visibility, and operations. Here’s how to approach the transition thoughtfully and sustainably:
1. Improve Demand Visibility First
Before cutting back inventory, ensure you have strong demand forecasting capabilities in place. JIT relies heavily on accurate, real-time demand signals—not broad projections. Start by tracking SKU-level sales patterns, seasonality, and order velocity across locations and channels.
2. Build a Reliable Supplier Network
Suppliers become strategic partners in a JIT system. Evaluate them based on their ability to deliver smaller quantities, more frequently, and on shorter lead times. For some businesses, this may mean shifting to more local or nearshore suppliers with tighter service-level agreements and backup options.
3. Invest in the Right Inventory Technology
Manual workflows won’t support JIT. You'll need an inventory management system that can automate reordering based on real-time consumption, sync with suppliers or ERP platforms, and offer visibility into inventory positions across multiple locations. The system should also allow for dynamic safety stock and reorder point adjustments.
4. Shift Operational Mindsets Internally
A successful transition requires more than tools—it needs buy-in from procurement, finance, and operations. JIT isn’t just about keeping inventory low; it’s about creating operational agility. Teams must be trained to think in terms of stock velocity, responsiveness, and supply chain resilience.
5. Start with a Controlled Pilot
Don’t roll out JIT across the board. Choose a set of fast-moving SKUs or a single warehouse with predictable demand to test the model. Monitor stockouts, order fulfillment rates, supplier reliability, and lead time performance. Use the pilot to identify risks, refine processes, and build internal confidence.
6. Scale Gradually With Feedback Loops
As your systems and teams mature, expand JIT to additional SKUs, product lines, or fulfillment nodes. Regularly review performance metrics like inventory turnover, fill rate, and split shipment rate to ensure the model continues to deliver value without compromising reliability.
Risks & Limitations of JIT (And How to Mitigate Them)
While Just-in-Time replenishment can make inventory leaner and operations more efficient, it also introduces exposure to certain risks. Because JIT operates with little to no buffer stock, disruptions—no matter how small—can ripple through the supply chain and affect fulfillment, customer satisfaction, or production schedules. Understanding these limitations is key to building a JIT system that’s both efficient and resilient.
Risk 1: Supplier Delays or Unreliability
When you're not holding excess inventory, you’re placing complete trust in your suppliers to deliver on time. A delayed shipment—even by a day—can result in stockouts, halted production, or unfulfilled orders.
How to mitigate it:
Establish strong SLAs (Service Level Agreements), work with multiple suppliers per SKU where feasible, and develop relationships with local or nearshore partners who can respond quickly. It’s also worth building a supplier scorecard to monitor performance over time.
Risk 2: Demand Spikes or Volatility
Sudden surges in customer demand can quickly exhaust lean inventory levels. In JIT systems, there's little buffer to absorb these spikes, which can lead to backorders or lost sales.
How to mitigate it:
Use real-time demand sensing tools and maintain a small dynamic safety stock for fast-moving or high-risk SKUs. Historical sales data, seasonality patterns, and promotions should be factored into replenishment triggers to make your system more predictive.
Risk 3: Transportation Disruptions
Even if suppliers are reliable, issues like shipping delays, customs holdups, or last-mile bottlenecks can still derail timely inventory arrival. Since JIT depends on tight delivery schedules, even minor transport disruptions can cause major fulfillment issues.
How to mitigate it:
Build transportation buffers into lead time estimates, partner with logistics providers offering guaranteed delivery windows, and avoid sole dependence on one shipping mode or route. For critical SKUs, consider holding minimal buffer stock at decentralized fulfillment nodes.
Risk 4: Internal Process or Communication Gaps
JIT requires close coordination between inventory, procurement, warehouse, and sales teams. Any misalignment—like late order approvals or inaccurate stock data—can delay replenishment and result in operational breakdowns.
How to mitigate it:
Ensure that your systems are integrated—so inventory, sales, and procurement teams all work off the same data. Automate reordering wherever possible and set up alerts for low-stock thresholds, missed delivery dates, or system mismatches.
Risk 5: Limited Flexibility in High-Complexity Environments
In businesses with wide product assortments, high customization, or long manufacturing cycles, JIT can become difficult to execute. Managing hundreds or thousands of low-volume SKUs with just-in-time logic can increase risk exposure rather than reduce it.
How to mitigate it:
Use a hybrid approach. Apply JIT to high-velocity or predictable SKUs, while using traditional or just-in-case models for long-tail items, critical components, or high-margin products that require more buffer.
How EasyReplenish Supports Just-in-Time Inventory Replenishment
Just-in-Time replenishment can’t run on spreadsheets, gut instinct, or disconnected systems. It requires real-time visibility, intelligent automation, and precise control over inventory movement. That’s exactly where EasyReplenish delivers.
With EasyReplenish, brands can build the backbone of a lean, demand-driven inventory strategy—without sacrificing reliability or operational confidence.
1. Real-Time Demand Visibility
EasyReplenish tracks sales velocity, reorder cycles, and inventory consumption across SKUs and locations in real time. This allows businesses to respond instantly to demand signals and automate replenishment as stock is consumed—no more delays or over-ordering based on outdated forecasts.
2. Dynamic Reorder Points & Smart Automation
Instead of fixed min-max rules, EasyReplenish uses dynamic reorder logic that adapts to actual sales patterns, supplier lead times, and stock availability. You can set location-level reorder triggers, prioritize high-velocity SKUs, and enable fully automated ordering workflows based on pre-defined rules.
3. Supplier Coordination Built-In
For JIT to work, supplier reliability matters. EasyReplenish integrates supplier lead times directly into replenishment calculations. You’ll know exactly when to reorder to ensure on-time delivery—down to SKU and location level. It also allows you to assign alternate suppliers and define custom SLAs per product.
4. Granular Safety Stock Controls
Unlike traditional systems, EasyReplenish doesn’t treat safety stock as a static number. It lets you define flexible buffers based on product volatility, demand variability, or strategic priorities—so you can stay lean without exposing your operation to frequent stockouts.
Centralized Intelligence Across Locations
Whether you operate one warehouse or ten, EasyReplenish provides centralized visibility into inventory performance across your entire network. You can monitor which SKUs are nearing depletion, which locations are at risk, and which replenishment cycles are underperforming—enabling proactive decisions and continuous optimization.
FAQs
Q1. How does JIT affect supplier relationships?
JIT increases the importance of supplier reliability and responsiveness. Since inventory is replenished in smaller quantities more frequently, delays or inconsistencies from suppliers can disrupt operations. Businesses using JIT often build stronger, more collaborative partnerships with suppliers and set clear delivery expectations backed by SLAs.
Q2. Can JIT be automated with inventory software?
Yes, and automation is critical to making JIT sustainable at scale. Platforms like EasyReplenish automate demand tracking, reorder point calculations, and replenishment workflows in real time. This ensures that stock is reordered precisely when needed, without manual effort or lag between consumption and replenishment.
Q3. How does Just-in-Time inventory replenishment work in the fashion industry?
In the fashion industry, JIT replenishment helps brands respond quickly to shifting trends without overcommitting to stock that may go out of style. Instead of producing large volumes upfront, fashion businesses can release smaller batches and reorder based on actual sales performance. This minimizes the risk of overstocking seasonal items, reduces markdowns, and ensures inventory stays fresh and relevant. For fast fashion or DTC brands, JIT also enables more frequent drops and better alignment between production, demand, and marketing cycles.
Optimize Your Inventory Effortlessly
Receive timely insights and updates to ensure your inventory stays perfectly aligned with demand.
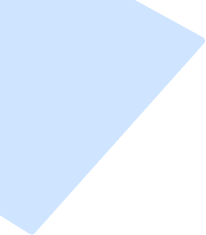
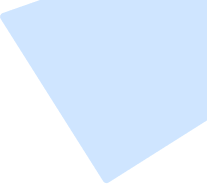
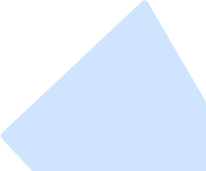
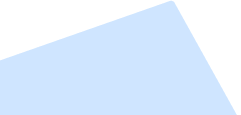